Liquid Air in Power and Transport Applications
Introduction
As we move to a low carbon energy and replace fossil fuels, we need new solutions to capture and “warehouse” green energy (wind turbines, solar, tidal, etc) and allow it to be used, when required, either on grid or in a vehicle. While the liquefaction of air to produce liquid nitrogen or liquid oxygen is a very mature industry, liquid air is a novel energy storage technology that could play an important role in the low carbon energy future. The UK has world-class expertise in both mechanical engineering and cryogenics.
"This is about harnessing an existing knowledge base for innovation. We are using mature technologies, but redeploying them in new and fast growing markets. This is cheaper and quicker to market, offering lower technology risk to the customer and new commercial opportunities to the existing supply chain and research institutions. It’s all there."
Toby Peters, founder LAENThe use of liquid air for grid-based energy storage could increase energy security, cut greenhouse gas emissions and create a new industry worth, for example, at least £1bn pa and 22,000 jobs to the UK. Liquid air technologies could also significantly increase the efficiency of road vehicles, particularly in commercial buses, vans and refrigerated lorry fleets; and again create additional revenue and jobs for the UK’s automotive industry.
Liquid Air is a pioneering solution to the problem of energy storage, which captures ‘wrong time’ or surplus energy – such as excess renewable energy produced at night when there is too little demand – storing it to provide peak time electricity and/or zero tail-pipe emission transport fuel.
It can be used in grid scale energy storage systems (Highview Power Storage has a pilot plant hosted by SSE at Slough) and a number of novel engine designs. The Dearman Engine is a piston engine that runs on liquid air while the Ricardo split cycle engine is a highly efficient diesel design that uses liquid nitrogen to capture heat from its own exhaust. Liquid air technologies are based on standard components and mature global supply chains, and there is an extensive cryogenic liquids distribution network in all industrialised countries. Liquid air technologies require no rare or expensive materials such as lithium or platinum.
Liquid air could in the short term:
- Strengthen energy security: a single gasometer-style tank of liquid air could make good the loss of 5GW of wind power for three hours - equivalent to almost 10% of the UK’s peak electricity needs.
- Smaller systems can be used to provide zero-emission back-up and reserve services, replacing diesel gensets (or new wires in the Grid).
- Reduce diesel consumption in buses and urban delivery vehicles by more than 20% using a liquid air Dearman Engine / diesel hybrid;
- Cut emissions from refrigeration on food lorries by 80%;
“We don’t have a globally significant battery industry in the UK, but we do have world-class cryogenics and mechanical engineering sectors. With the right support from government, Britain could steal a march in this technology and capture many of the jobs it would create.”
Dr Andy AtkinsRicardo
It also raises the possibility of zero-emission liquid air city cars filling up at road-side forecourts at a fraction of current fuel costs and with lower lifecycle vehicle emissions than either electric or hydrogen powered vehicles.
With ‘wrong-time’ energy from renewable generation a growing challenge to the electricity grid, there is real demand for affordable large scale energy storage solutions both in the UK and abroad. Liquid Air Energy Storage plants would be built from standard industrial equipment and technologies and can therefore be rapidly deployed. In the UK, such a network could develop into a business worth at least £1bn per year by 2050 and create 22,000 jobs. This excludes its potential economic value in the transport sector.
Why do we need Liquid Air as a new energy vector/storage solution?
Energy strategy over the past decade has sought to improve generating technologies so they can provide energy more cheaply and reliably, and with lower CO2 emissions. How that energy is used has traditionally been overlooked, but this is now changing. Energy efficiency is becoming a mainstay of policy, and so is the management of energy systems.
Greater emphasis is being placed on the use of technologies that can make best use of the renewable energy that is being produced. Turning the instantaneous power generated by a wind farm or solar array into energy vectors to store it, allowing the use of that power at a different time or place, can increase the efficiency and reduce the costs and CO2 of the whole energy system.
Existing energy stores / vectors – batteries, pumped hydro, hydrogen – while part to the solution, all suffer significant drawbacks, which are being increasingly exposed by the rapid shift to intermittent renewable energy. While in no way claiming to be a panacea to all our energy challenges, liquid air as an energy store has different attributes for which there is a real demand in a robust low carbon power and transport infrastructure.
What is liquid air?
Air can be turned into a liquid by cooling it to around -196C using standard industrial equipment. 700 litres of ambient air becomes about 1 litre of liquid air, which can then be stored in an unpressurised insulated vessel. When heat (including ambient or low grade waste heat) is reintroduced to liquid air it boils and turns back into a gas, expanding 700 times in volume. This expansion can be used to drive a piston engine or turbine to do useful work. The main potential applications are in electricity storage, transport and the recovery of waste heat. Liquid air or liquid nitrogen could be used in a number of emerging technologies including:
- The Liquid Air Energy Storage (LAES) system developed by Highview Power Storage, a plant which generates liquid air using cheaper, off-peak electricity, stores it for some hours or days, and then expands it through a turbine to deliver power back to the grid at times of peak demand.
- The Dearman Engine, a novel piston engine that runs on liquid air or nitrogen, which could be used either as a prime mover (main engine) or as a secondary unit to recover waste heat from an internal combustion engine (ICE) to raise efficiency
- The Ricardo split cycle engine, a novel diesel engine design that incorporates liquid nitrogen to increase efficiency by capturing its own exhaust heat.
History
The idea of liquid air as a energy vector is not new. Scientists first liquefied air in 1883, and within 20 years the Liquid Air Car Company had produced a vehicle that would run on it. While various prototypes were produced over the years, the engines were always very inefficient and could not compete. It was not until the first decade of the 21st century with the search for new zero emission energy vectors that a British inventor from Bishop’s Stortford demonstrated the critical breakthrough.
Liquid Air Car in 1903, New York Times
Harnessing waste heat
Liquid air is uniquely capable of converting low grade waste heat into power at very high levels of efficiency, ~50%, because of its low starting temperature (-196C). This compares favourably to other waste heat recovery technologies whose maximum theoretical yields are limited to about 20% at 100°C. The liquid air cycle works between -196C and ambient temperatures, meaning the addition of even low grade waste of less than 100C, which is otherwise difficult to exploit, can increase the work output significantly. Sources of low grade waste heat that could be exploited by liquid air technologies include vehicle engines, power generation and industrial processes.
- In the UK, industrial waste heat amounts to as much as 40TWh per year - enough to heat 2.4 million homes. Industrial demand for heat is easily large enough to absorb this, but individual sources of supply and demand rarely coincide in time or place. Even if all opportunities to make use of waste heat as heat were exploited, there would still be very substantial amounts available to generate electricity.
- In transport, ~30% of the energy content of a litre of fuel is rejected through the radiator coolant loop. The Dearman Engine can be deployed as a high yield thermal energy recovery system that could convert heat from the exhaust or coolant systems of an IC engine into shaft power at practical conversion efficiencies of up to 50%. This would increase the overall engine efficiency by between 20% and 30% without impacting on any other fuel efficiency technologies.
Safety
Cryogenic liquids present manageable hazards which are well understood. While these hazards are serious, their risk of occurring is minimised by the way in which early liquid air commercial vehicles will be deployed. The main hazards and their remedies are shown in the table below.
Hazard | Mitigation |
Extreme cold. Both liquid air and liquid nitrogen are profoundly cold, meaning they can cause serious cold burns and frostbite if they come into direct contact with the skin. Injuries can also occur if someone touches an uninsulated tank or pipe. | The highest risk of contact would be during re-fueling, but this risk would be eliminated by driver training, protective clothing and insulated fuel pipes which lock to the vehicle fuel tank. Such re-fueling systems are already in use (see picture) for liquid nitrogen and Liquefied Natural Gas (LNG). |
Asphyxiation. If liquid nitrogen is used as a transport fuel, the exhaust is clean but unbreathable, making it unsuitable for use indoors. A vehicle left idle for long periods in a poorly ventilated garage might also present a hazard since the liquid nitrogen in the fuel tank would slowly evaporate, potentially raising the concentration of nitrogen in the atmosphere. | All the currently proposed applications of liquid air technologies are commercial vehicles that spend their working lives outdoors, largely eliminating the risk. If vehicles equipped with liquid nitrogen are to spend any time indoors (e.g. for servicing) the hazard could be eliminated with monitoring, ventilation and safety protocols. Liquid air would not present this hazard. |
Oxygen enrichment. Liquid air consists of oxygen and nitrogen in the same proportions as in the atmosphere: 79:21. However, because nitrogen boils at a lower temperature (-196C) than oxygen (-183C), over time liquid nitrogen boils off preferentially and the proportion of oxygen in liquid air can rise. Since oxygen is highly reactive, particularly if it comes into contact with hydrocarbons for example, any concentration above 23% is regarded as dangerous. | All the proposed applications are likely to use an entire tank of liquid air each day, so reducing the chance of enrichment. Again, monitoring equipment and fail-safe systems would minimise the risk. It should be noted that the Liquid Air Energy Storage plant in Slough has operated safely for two years (pictured). Liquid nitrogen does not present this hazard, and there is enough spare nitrogen capacity to fuel early applications until at least 2019. |
A full discussion of hazards and mitigation can be found in the CLCF report, Liquid air in the energy and transport systems.
Liquid Air - Key advantages
- A superabundant and cost-free feedstock;
- Cryogenic liquid production, its distribution infrastructure and its equipment supply chain are already mature;
- Storage is at low pressure and there is no fuel combustion risk;
- For grid based storage, no geographical constraints as with pumped hydro or large scale CAES (compressed air energy storage); and can be deployed at scales batteries find heard to achieve
- None of the proposed technologies requires scarce materials;
- The energy density of liquid air compares favourably to low-carbon competitors;
- For transport applications, very fast re-fuelling times are possible ;
- Cost competitive to other low-carbon technologies;
- Synergy with other processes, including use of waste heat (acting as a high yield heat energy recovery system) and/or provision of cold.
Grid electricity
Highview Power Storage pilot plant at Slough
The debate around grid balancing is usually presented in terms of the need for additional gas fired plant to run when the wind drops. But there is powerful case for additional grid storage to absorb excess wrong time energy and warehouse it for when required, in which liquid air could play a major part.
As wind capacity increases, there will be increasingly frequent periods when wind output exceeds demand, and wind farms have to be switched off even though the wind is blowing. This is already happening in Texas, Germany and the UK. So far the problem has largely been caused by local bottlenecks in transmission lines, but if wind capacity grows as forecast, off-peak wind generation could often exceed total demand.
In these conditions storage has a major advantage over gas and other forms of balancing capacity as it can absorb energy as well as discharge. This will become increasingly valuable to the grid by preventing the waste of ‘wrong time’ energy, and by allowing fossil power plants to run more efficiently.
In this context, Liquid Air Energy Storage (LAES) could:
- provide network operators and energy companies a cost effective and scalable means of time-shifting large amounts of energy to help balance the grid
- deliver investment savings by allowing upgrades of transmission and distribution networks to be deferred, and eliminating grid bottlenecks
- reduce CO2 emissions from grid electricity by 1) capturing excess off-peak (‘wrong time’) renewable energy and using it to displace high-emitting peaking generators, and 2) allowing fossil power plants to run more efficiently at full load rather than ramping up and down to compensate for variable wind output
- provide strategic levels of electricity storage: a single gasometer-style tank of the capacity currently used in the LNG industry could store sufficient energy as liquid air to compensate the loss of 5GW of wind power for 3 hours – equivalent to almost 10% of peak UK electricity demand.
Transport
"Specifically, the Dearman Engine has advantages as a prime mover for lower utilisation indoor materials handling vehicles (e.g. forklifts) and for underground mining vehicles. For heat recovery, there are advantages in bus and light truck applications, especially where there is also a requirement for onboard cooling of passengers or loads.”
E4 Tech
Transport of people and goods is generally considered as a distinct category within the wider energy debate. Not only is it a discreet economic bloc responsible for more than a third of all energy consumed in the UK, but it also places unique demands on the energy vectors deployed. Progress on existing vectors such as biofuels, electric vehicles (EVs) and hydrogen fuel cell vehicles (FCVs) is proving far slower than expected or required by policymakers. Analysis reveals that liquid air could provide an attractive low carbon energy vector in several vehicle types and functions:
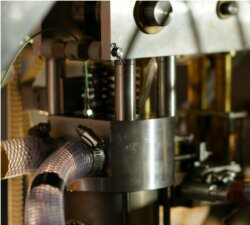
"A key advantage is that because the engine never gets hot, it can be built of very different materials from today’s motors. You can imagine the engines being fabricated out of low-cost alloys or plastics, something very cheap and light and that would have a major impact on the price of the vehicle”
Colin Garner, Professor of Applied Thermodynamics at Loughborough University- Prime mover: a cryogenic engine such as the Dearman Engine produces zero emissions at the point of use; is non-combustive; has energy and power density on a level with battery electric technology; and has the potential for rapid refuelling. This makes it potentially attractive as a ‘prime mover’ (main engine) for scooters, city cars, short range vans and boats, but also, for example, forklift trucks and mining equipment.
- Heat hybrid: a cryogenic engine such as the Dearman Engine could also be used as a ‘heat hybrid’ in combination with an internal combustion engine or hydrogen fuel cell, to convert waste heat into additional shaft power at high levels of efficiency, reducing both fuel consumption and emissions. This approach could cut diesel consumption in buses and lorries by 25%.
- High efficiency internal combustion engine: heat recovery could also be achieved using the Ricardo split cycle engine, a novel internal combustion engine design that incorporates liquid nitrogen to capture exhaust heat and increase fuel efficiency in lorries. Detailed modelling suggests efficiencies of more than 60% are possible, compared to around 40% for modern diesel engines.
- Refrigerated food transport: some food delivery vehicles already use liquid nitrogen to provide refrigeration, but fail to capture any additional shaft power from the nitrogen evaporation process. We calculate that a vehicle food refrigeration system using liquid nitrogen or liquid air to provide both additional shaft power and cooling would cut emissions by almost 80% on the basis of current grid average electricity.
Liquid air production and cost
Liquid air is not produced commercially today since demand is for the individual components of air (primarily nitrogen and oxygen). However liquid nitrogen, which makes up 78% of air, and is interchangeable with it as an energy vector, is a readily available product. The industry sells some 8,000 tonnes per day in the UK, which is largely distributed by road tanker. The distribution network covers almost the whole country, and could certainly be used to support early deployment of ‘liquid air’ applications.
The chart above shows the location of existing industrial gas production sites; potential new production sites at LNG import terminals; and the depots of some significant hauliers and supermarket chains, who may be early users of long-haul liquid air applications. Each production site is marked with a radius of 50 and 100 miles to show its potential delivery catchment area. It is clear that most of the UK is covered by existing or potential liquid air distribution, and the existing distribution network are more than adequate to supply the short to medium term fuel needs of an emerging ‘nitrogen economy’.
In fact, the industry inevitably produces excess gaseous nitrogen, because there is four times as much nitrogen as oxygen in the atmosphere but much less demand for it commercially. Spiritus Consulting estimates conservatively that the industry vents at least 8,500tpd of excess nitrogen gas to the atmosphere every day. This could instead be liquefied and used in place of liquid air to fuel the equivalent of 6.5 million car kilometres daily.
Producing liquid air directly would be cheaper than producing liquid oxygen and nitrogen separately since the process consumes about a fifth less energy. It has been calculated that liquid air as a transport fuel could be produced for as little as 2.5 pence per litre, on the basis of current electricity prices. For a small Dearman Engine vehicle that would translate to fuel costs of 6 pence per kilometre, compared to 10 pence (including tax) for a petrol car of average efficiency.
Manufacturing and pathways to deployment
Liquid air devices can generally be made substantially from existing components drawn from mature supply chains with few bottlenecks to hamper expansion. And unlike many other low carbon technologies - such as EVs - liquid air technologies require negligible rare earth metals and other scarce resources.
The Liquid Air Energy Storage system is made entirely from existing components drawn from the industrial gases and power generation industries, and a substantial proportion of a LAES plant could be also sourced from UK suppliers. If design, civil engineering and construction work were added to domestically produced components, around 50-60% of the value of a LAES installation could originate in the UK. There is no reason why the international supply chain should not deliver a target of 500MW of LAES capacity in the UK by 2020, or supply a potential UK market of 14GW by 2050.
In transport, the Dearman Engine is a piston engine that operates at near ambient temperatures, and as a result it is unlikely to offer many unfamiliar challenges to vehicle engine manufacturers. The most unfamiliar part of the system is likely to be the part exposed to cryogenic working fluid – liquid air or nitrogen. However, cryogenic technologies are mature and have been used in the industrial gas and LNG industries for decades. In the short term it is expected that the Dearman engine would have similar capital costs and embedded carbon to a conventional ICE, and significantly lower than EVs or FCVs.